You’re running a busy healthcare facility. Every day, patients rely on you for accurate diagnoses, safe treatments, and quality care. But sometimes, things go wrong. A patient waits too long for test results. These small errors can quickly turn into big problems.
You address each issue as it comes, but somehow, they keep happening. It feels like you’re putting out fires instead of solving the root cause. This is frustrating for you, your team, and — most importantly — your patients.
Here’s the truth: quick fixes won’t cut it.
You need a system to identify problems, find out why they happen, and stop them from recurring. That’s where the Corrective and Preventive Action (CAPA) process comes in. CAPA process in healthcare helps you dig deep, fix issues for good, and improve your processes over time.
With an effective CAPA process, you don’t just patch things up. You build a stronger, safer system that patients can trust. Your team works better, and everyone feels confident knowing that problems are addressed properly.
In this guide, you’ll learn how to implement CAPA step-by-step. You’ll see how CAPA can transform patient care, improve safety, and create a culture of continuous improvement. By the end, you’ll have a roadmap to make your facility more efficient, reliable, and patient-centered.
Let’s get started.
TL;DR
-
CAPA is a systematic approach used in regulated industries like healthcare and medical devices to identify, fix, and prevent quality issues, ensuring patient safety and compliance with quality standards.
-
The CAPA process includes problem identification, taking immediate action, conducting root cause determination, developing a CAPA plan, implementing it, verifying effectiveness, and maintaining a well-documented process for internal audits.
-
An effective CAPA system improves product quality, reduces failure modes, and ensures timely issue resolution. It supports a culture of continuous improvement, helps facilities meet regulatory requirements, and enhances patient satisfaction.
-
Zonka Feedback streamlines the CAPA process by automating patient feedback collection, assigning tasks, tracking actions, and ensuring issues are resolved efficiently. Schedule a demo to experience seamless CAPA management and stay audit-ready.
Turn Patient Feedback into Actionable Insights💡
Track, analyze and resolve issues in real-time with an all-in-one platform. Start your free trial and experience the power of efficient CAPA management!
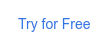
What is CAPA Process and Why it Matters in Healthcare?
In healthcare, ensuring patient safety and maintaining high standards is non-negotiable. This is where the Corrective and Preventive Action (CAPA) process plays a crucial role. CAPA is a systematic approach designed to identify problems, fix them, and prevent them from happening again.
- Corrective Action focuses on fixing identified problems and addressing their root causes.
- Preventive Action focuses on identifying potential issues and implementing measures to stop them before they occur.
By addressing both existing and potential problems, CAPA creates a framework for continuous improvement and safer healthcare delivery. Here you’ll find real-world examples of how the CAPA process is applied in the healthcare industry.
What is the Purpose of CAPA Process in Healthcare?
The CAPA process exists to make sure everything runs smoothly, safely, and with a focus on improvement. It helps organizations catch problems before they spiral, fix them for good, and stop them from happening again. Here’s how CAPA makes a difference:
- Fix Existing Problems: Whether it’s a process error, a mistake, or something not working as it should, CAPA helps you identify and resolve it effectively.
- Prevent Future Issues: It’s not just about solving today’s problem — CAPA looks ahead to spot potential risks and eliminate them before they turn into real issues.
- Improve How Things Work: CAPA enhances your systems and workflows, creating smoother, more efficient processes that drive continuous improvement.
- Stay Compliant: Regulatory standards aren’t just about paperwork — they ensure quality and safety. CAPA helps you meet these requirements confidently.
- Keep Patients Safe and Happy: Fewer errors mean safer care. By improving processes, CAPA also helps build trust and deliver a better patient experience.
At its core, CAPA isn’t just about solving problems — it’s about creating a culture of quality. It gives your team a clear, structured way to prevent recurring issues, meet high standards, and build trust with the people you serve. With CAPA, you’re not just fixing things; you’re setting the foundation for lasting excellence.
Benefits of an Effective CAPA Process
An effective CAPA process offers significant benefits for healthcare facilities:
- Keep Patients Safe: When you identify and fix problems at their core, patients stay safer. CAPA helps you prevent risks, so safety isn’t left to chance.
For example, if a hospital discovers recurring medication errors due to mislabeled bottles, CAPA ensures the root cause is fixed by improving label verification protocols—and preventing future incidents. - Provide Better Care: Fixing issues and improving processes means patients get better care. There will be fewer mistakes, smoother experiences, and better health outcomes.
For instance, reducing diagnostic delays by implementing a new scheduling system can lead to quicker test results and better health outcomes. - Stay Compliant: Meeting standards like NABH or FDA becomes easier with CAPA. It keeps you audit-ready, helps you avoid penalties, and shows your commitment to quality.
- Stop Problems from Repeating: CAPA goes beyond quick fixes. It digs deep to find the real cause and implements solutions. This way, the same issue won’t happen again, saving you time and frustration.
For example, a recurring shortage of critical supplies might stem from a flawed inventory system. CAPA can establish robust stock monitoring to prevent future shortages. - Build Trust with Patients: When you take patient concerns seriously and make real changes, they trust you more. It shows you’re listening and always improving.
- Hold Everyone Accountable: CAPA ensures everyone knows their role in fixing problems. Clear tasks and timelines keep things on track, and nothing gets missed.
For example, a task force might be created to address equipment failures, with each team member responsible for specific corrective measures. - Make Processes Smoother: By fixing inefficiencies, CAPA helps things run smoothly. Your staff will spend less time dealing with recurring issues and more time caring for patients.
- Make Better Decisions: CAPA relies on facts, not guesses. You’ll make smarter decisions based on solid data and thorough investigations.
For instance, feedback data showing dissatisfaction with cafeteria hygiene might prompt a review of cleaning protocols, backed by actionable recommendations. - Encourage Teamwork: CAPA often involves different departments working together. It improves communication and helps your team solve problems as one unit.
- Create Continuous Improvement: CAPA builds a culture where you and your team always look for ways to get better. Every problem becomes a chance to improve patient care.
Implementing CAPA ensures your facility continuously improves, providing reliable, safe, and high-quality healthcare.
How CAPA Support NABH Compliance?
To meet NABH accreditation standards, healthcare facilities must prioritize patient safety, quality care, and continuous improvement. The CAPA process plays a pivotal role in achieving these goals. By addressing systemic issues effectively, CAPA ensures that healthcare providers align with NABH requirements.
CAPA contributes to NABH compliance by:
-
Identifying Quality Issues: CAPA processes help uncover problems related to clinical care, safety incidents, or patient complaints.
-
Addressing Root Causes: CAPA ensures that issues are resolved at their source by conducting thorough root cause analyses.
-
Preventing Recurrences: Implementing preventive measures reduces the chances of repeat errors, aligning with NABH’s focus on continuous quality improvement.
-
Documenting Actions: Detailed CAPA records serve as evidence during NABH audits, demonstrating the facility’s commitment to resolving and preventing issues.
Without CAPA, facilities risk non-compliance, safety breaches, and compromised patient care. By integrating CAPA into daily operations, healthcare providers can confidently meet NABH standards and deliver safe, effective, and reliable healthcare services.
A Step-by-Step Walkthrough of the CAPA Process
Here are the CAPA process steps to help you achieve NABH compliance. The CAPA process flow chart typically includes steps like identifying the problem, conducting root cause analysis, developing an action plan, and verifying effectiveness.
Step 1: Spot and Address Issues Before They Escalate
A patient complains about a long wait time for test results. Another patient mentions a mix-up in medication. These seem like isolated incidents, but they may point to deeper issues in your processes. Recognizing these problems early is crucial to prevent risks to patient safety.
Problems can appear as deviations from procedures, nonconformities, or patient complaints. Collecting patient feedback through multiple channels helps you spot these issues quickly.
Tools like Zonka Feedback make it easier to gather feedback via in-app surveys, email surveys, kiosk surveys, and SMS survey follow-ups. This real-time data collection helps track complaints seamlessly. By analyzing feedback, you can distinguish isolated incidents from recurring problems that require corrective action.
Sentiment analysis further reveals patterns in patient dissatisfaction. It helps identify underlying causes by analyzing the emotions and intent behind feedback. Dashboards and reports offer a clear view of trends, making it easier to decide when to initiate CAPA.
Early identification sets the stage for effective corrective and preventive actions. This ensures your healthcare facility remains compliant, responsive, and focused on continuous improvement.
Step 2: Take Immediate Action
Once a problem is identified, the next step is to act quickly to contain it. Immediate action prevents the issue from escalating and causing further harm.
Containment measures can include stopping a procedure, isolating faulty equipment, or correcting an administrative error. These temporary actions help stabilize the situation until a full investigation can be carried out.
Using tools like Zonka Feedback, you can receive automated alerts for critical feedback. These alerts ensure that urgent issues are flagged instantly so the right teams can respond without delay. Quick action helps reduce risks, protect patient safety, and maintain operational efficiency.
Immediate action doesn’t address the root cause, but it controls the damage and buys time for a thorough corrective and preventive plan. This step is essential for ensuring patient safety and meeting NABH compliance requirements.
Step 3: Conduct Root Cause Analysis
After taking immediate action, it’s time to identify the root cause of the problem. Without understanding the underlying issue, the same problems will continue to arise.
Use methods like the 5 Whys (asking “Why?” repeatedly to drill down to the core issue), the Fishbone Diagram (mapping potential causes by categories), or Fault Tree Analysis (breaking down events that led to the problem). These techniques help ensure you’re not just addressing symptoms but the actual cause.
For example, let’s say a patient experienced delayed test results. Applying the 5 Whys method:
- Why were the patient’s test results delayed?
The laboratory technician did not process the samples on time.- Why did the technician not process the samples on time?
The testing equipment was not operational.- Why was the testing equipment not operational?
Preventive maintenance was not performed as scheduled.- Why was preventive maintenance not performed?
The maintenance schedule was overlooked by the facility management team.- Why was the schedule overlooked?
There was no automated system to track and alert the team about maintenance deadlines.
By using the 5 Whys, you discover that the root cause is the staff shortage, not just a labeling error.
Identifying the root cause is just the beginning. To ensure your investigation is thorough and your findings lead to meaningful improvements, you need a systematic way to document, track, and act on each step. This is where CAPA software comes in — it streamlines the entire root cause analysis process, making sure nothing falls through the cracks.
How does CAPA Software Support Root Cause Analysis?
-
Clear and Complete Documentation: CAPA software helps you keep track of every detail in the investigation process — from the initial problem to the final findings. Everything is recorded step-by-step, so nothing gets lost or overlooked.
-
Assign Tasks to the Right People: You can easily assign investigation tasks to team members who know the process best. The software sends reminders and tracks progress, so everyone stays on top of their responsibilities.
-
One Place for Everything: All your investigation data — notes, evidence, reports, and actions — are stored in one secure place. When it’s time for an audit or a review, you don’t need to scramble for information; it’s all organized and easy to access.
-
Real-Time Tracking: CAPA software gives you a clear view of what’s happening in real time. If a task is delayed or something isn’t progressing, you’ll know immediately and can step in to keep things moving.
-
Easy Collaboration Across Teams: Issues in healthcare often involve different departments. CAPA software makes it simple for quality teams, operations staff, and clinical personnel to work together, ensuring everyone’s input is considered for a well-rounded investigation.
-
Transparency and Accountability: Every action taken is logged, showing who did what and when. This transparency helps build trust and ensures that everyone is accountable for their part in solving the problem.
By using CAPA software, healthcare teams can uncover the real reasons behind issues, not just fix the surface-level symptoms. This helps you stop problems from recurring, protect patient safety, and meet NABH compliance standards. It’s about making sure your processes get better and your patients get the safe, high-quality care they deserve.
Step 4: Develop an Action Plan
You’ve identified the root cause — now it’s time to fix the problem for good. You need a clear plan to solve this issue and ensure it doesn’t happen again.
Start by outlining specific actions. In this case, you might decide to hire additional staff, update your scheduling system, and train your team on managing appointments effectively. Assign responsibilities to the right people: the HR manager for hiring, the operations team for updating the system, and the clinical lead for staff training. Set realistic timelines to keep everyone accountable and on track.
But how do you make sure things are improving?
Zonka Feedback helps you track patient concerns and monitor the results of your actions. If patients start reporting shorter wait times, you know your plan is working. If not, you can quickly adjust.
A strong action plan isn’t just about solving today’s problem — it’s about creating a system that learns and improves. When everyone knows their role and progress is tracked, your healthcare facility stays efficient, compliant with NABH standards, and focused on delivering great patient care.
Step 5: Turn Plans into Action for Real Improvement
A plan is only as good as its execution. Now that you have your corrective and preventive actions outlined, it’s time to implement them. Whether your plan involves hiring new staff, improving scheduling systems, or conducting training, efficient execution is critical.
Ensure each team member understands their responsibilities. Hold brief meetings to clarify tasks, expectations, and deadlines. Consistency is key — corrective and preventive measures must be followed precisely to be effective.
CAPA software streamlines task assignments, tracks progress, and automates follow-ups to ensure nothing is missed. For example, if the operations team is updating scheduling systems, the software tracks progress and sends reminders to keep tasks on schedule.
Step 6: Verify the Effectiveness of Your Actions
Once you’ve implemented your corrective and preventive actions, the next step is to ensure they’ve worked. Simply put, you need to measure success. Did the changes actually resolve the issue, or is the problem still lingering?
That's why taking follow-up is essential. For example, if the corrective action addressed long wait times, compare current wait times to previous ones. Use Zonka Feedback to collect targeted follow-up feedback from patients through patient satisfaction surveys. Ask specific questions related to the issue: “Was your wait time shorter during your last visit?” or “Did you receive your medication correctly?”
Analyze the feedback and data carefully. If patients report improvements and the data shows positive trends, your corrective actions worked. If not, identify what went wrong and refine your approach. This verification step is essential for maintaining NABH compliance and ensuring your facility continuously improves in delivering safe, high-quality care.
Step 7: Seal the Deal with Proper Documentation
Thorough documentation is the final step in the CAPA process. Proper records ensure accountability, transparency, and readiness for NABH audits. Without clear documentation, even the best corrective actions can fall short.
Document every detail: what the issue was, what caused it, the actions taken, who was responsible, and the outcomes. Comprehensive reporting is key for audit readiness. Detailed CAPA documentation demonstrates to NABH auditors that your facility takes continuous improvement seriously. It shows that issues are identified, resolved, and prevented from recurring.
Closing the CAPA process with proper documentation ensures you’re not just fixing problems temporarily but creating a culture of lasting quality and patient safety.
Now that you know the entire CAPA management process, let's have a glance at the challenges.
Common Challenges in CAPA Implementation
Implementing the CAPA process isn’t always straightforward. Many healthcare facilities struggle with missteps that can undermine their effectiveness. Below are some of the most common challenges, along with how you can overcome them to ensure smoother CAPA execution.
1. Focusing on the Wrong Issues
One of the biggest pitfalls is treating every issue as CAPA-worthy or ignoring problems that genuinely need it. CAPA should focus on systemic issues that affect processes, patient safety, or quality — not isolated incidents.
Zonka Feedback helps distinguish recurring issues from one-off complaints by analyzing patterns in patient feedback. This allows you to prioritize systemic problems that truly require CAPA.
2. Internal Biases and Politics
Internal biases or political dynamics can delay CAPA implementation or skew root cause analysis. Cross-functional teams and clear communication are critical to ensure an unbiased investigation and resolution.
Zonka Feedback provides real-time, data-driven insights that leave no room for subjectivity. Feedback can be shared across teams, encouraging a transparent and collaborative problem-solving process.
3. Setting Unrealistic Timelines
Setting overly ambitious timelines can overwhelm teams and result in incomplete CAPA steps. Achievable goals ensure the CAPA process is carried out effectively without compromising on quality.
Zonka Feedback streamlines task assignments and follow-ups, helping teams stay organized and on track. Automated reminders ensure actions are completed on time without adding unnecessary pressure.
By addressing these challenges proactively, healthcare facilities can create a CAPA process that is focused, unbiased, and manageable. This ensures improved patient safety, compliance with NABH standards, and long-term quality enhancement.
Best Practices for CAPA in Healthcare Facilities
To make CAPA effective and impactful, healthcare facilities must focus on building a culture of improvement, empowering their staff, and using the right tools. Here are the best practices to ensure CAPA drives real, lasting results:
-
Build a Culture of CAPA: Encourage teams to treat CAPA as an opportunity to improve, not just a process to follow. Promote proactive problem-solving where employees feel comfortable identifying issues and suggesting solutions. A strong CAPA culture turns everyday challenges into opportunities to strengthen processes and improve patient care.
-
Regular Training for Staff: Training is key to making CAPA effective. Equip your staff with the knowledge and skills to identify problems, perform root cause analysis, and implement corrective actions. Regular sessions ensure everyone understands their role in problem-solving and the steps involved in CAPA. Well-trained staff can act quickly and effectively when issues arise.
-
Use Technology to Enhance Efficiency: Technology can streamline CAPA management, saving time and effort. Tools like Zonka Feedback automate feedback collection, identify recurring issues, and track corrective actions. Automated follow-ups ensure tasks are completed on time while providing clear records for monitoring progress.
By adopting these best practices, healthcare facilities can build a CAPA system that is efficient, proactive, and focused on continuous improvement. To truly embed these best practices into your CAPA process, you need the right tools.
Managing CAPA manually can be challenging, but CAPA software simplifies and streamlines the process, ensuring your efforts lead to consistent and effective outcomes.
Why Use CAPA Software?
Implementing the CAPA process in healthcare manually can be time-consuming, error-prone, and difficult to manage. CAPA software simplifies this process by offering automation, organization, and real-time monitoring. Here’s why healthcare facilities should consider using CAPA software:
-
Automation: Reduces manual effort by automating routine tasks like assigning actions, sending reminders, and tracking progress. This minimizes errors and ensures nothing falls through the cracks.
-
Centralized Documentation: Stores all CAPA records in one secure place, making it easy to access information when needed. This is particularly helpful during audits, where comprehensive documentation is essential for demonstrating compliance.
-
Real-Time Tracking: This allows you to monitor the progress of CAPA activities as they happen. This ensures that corrective and preventive actions are completed on time and helps identify delays before they become an issue.
-
Reporting and Analytics: Provide insights into trends, effectiveness, and areas that need improvement. Detailed reports help you evaluate the success of your CAPA efforts and make data-driven decisions to enhance patient safety and quality.
Using CAPA software streamlines the entire process, making it more efficient, organized, and effective. This helps your facility stay on track with quality improvements and ensures issues are resolved quickly and thoroughly.
Zonka Feedback and CAPA Software: The Perfect Duo for CAPA Management
Managing a CAPA system manually can be overwhelming — tasks slip through, delays happen, and patient complaints go unresolved. This not only impacts patient safety but also threatens your facility’s compliance with quality standards.
To tackle these challenges, combine Zonka Feedback and CAPA software. Zonka Feedback captures real-time patient concerns and helps you follow up effectively, while CAPA software manages tasks, documentation, and timelines to ensure issues are resolved efficiently. Together, they help you identify, act on, and prevent problems — creating a safer, more reliable healthcare experience.
Here’s how these tools work together to streamline your CAPA process:
- Identify Issues Quickly: Use Zonka Feedback to capture patient complaints through emails, surveys, kiosks, or SMS. This helps you spot issues that need corrective action.
- Initiate a CAPA Request: When feedback signals a deeper problem, use CAPA software to create a CAPA request and kickstart the resolution process.
- Assign and Track Tasks: CAPA software helps you assign tasks to the right team members, track progress, and set deadlines to ensure timely action.
- Close the Feedback Loop: Communicate with patients through Zonka Feedback and document responses. Let them know their concerns are being addressed.
- Document Everything Clearly: Keep detailed records of investigations, actions, and outcomes in CAPA software for easy access during audits.
- Measure Effectiveness: Track patient feedback with Zonka Feedback to see if your corrective actions are working. CAPA software ensures nothing falls through the cracks.
- Analyze Trends and Improve: Use analytics from both tools to identify patterns, root causes, and areas for improvement.
Ready to build an effective CAPA system that ensures continuous improvement and regulatory compliance? Get started with Zonka Feedback and transform how your facility handles CAPA procedures and patient feedback.